Feeder breaker, as a core crushing equipment in the coal mining and other fields, directly affects the processing capacity and operating costs of the production line. This article will delve into how the collaborative optimization of static grid screening and dynamic screen shaft technology can comprehensively improve the equipment's output, energy efficiency, and reliability. It will also propose systematic upgrade strategies based on industry practice data and technological innovation trends.
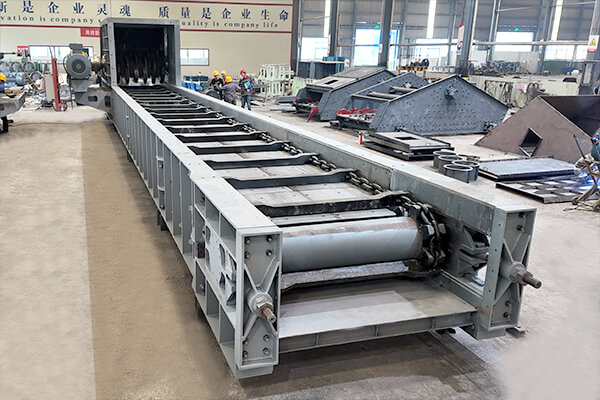
The combined application of static grid screening and dynamic screen shaft essentially integrates and optimizes the three-stage process of "Coarse screening - fine screening - crushing". The static grid screen, as the first barrier, quickly separates qualified materials or oversized rocks that do not require crushing through fixed screen holes (typically 50-150mm), reducing unnecessary crushing energy consumption. The dynamic screen shaft, through vibration or rotation screening (screen holes 5-30mm), performs secondary classification on the materials entering the crushing chamber, ensuring uniform particle size, reducing hammer wear, and improving the quality of the output. The synergy of the two can reduce the energy consumption per ton of
feeder breaker by 15%-20%, while extending the lifespan of vulnerable parts by more than 30%.
The receiving section adopts static screening, while the non-receiving section uses dynamic screening devices. The non-receiving section employs sinusoidal disturbance screening to prevent any material blockage (including unbreakable iron objects, etc.).
The static screening grating screen is fixed on the conveying box by rails, which is suitable for the screening of large particle materials.
The feeder breaker material receiving section adopts static screening method, the static screening grate is fixed on the conveyor box by the rail, which is suitable for the screening of large particle materials.
The non-material receiving section adopts dynamic screening method. Integrate a specially designed sinusoidal disturbance screen on the conveyor box, which is suitable for screening small particles and sticky materials. The non-receiving section adopts sinusoidal disturbance screening method to prevent any material from getting stuck.
The material is pre-screened and then crushed, which can avoid excessive crushing and reduce the production of powder, maximize the yield of mineral blocks, and improve the economic benefits and value of end users.
The collaborative innovation of static grid screening and dynamic screen shaft not only enhances the performance of
feeder breaker but also promotes the evolution of the crushing process towards higher efficiency and intelligence.