The
coal roller screen is an efficient screening device composed of side-by-side screen shafts. Through the crossed screen discs, misaligned screen holes are formed, thereby achieving effective screening of coal. If the output particle size of the coal roller screen is too large, it will cause great problems in the subsequent conveying links and even lead to shutdown accidents.
A certain power company changed the chain coal feeder of Furnace No. 1 to a belt coal feeder. The inlet particle size of this belt coal feeder is 50mm. Due to the fact that the lumps of coal at the inlet sometimes have a relatively large particle size, the belt of the belt coal feeder was repeatedly scraped by the large lumps of coal during operation. The lumps of coal got stuck between the inlet material guide trough and the belt of the coal feeder, causing a shutdown accident.
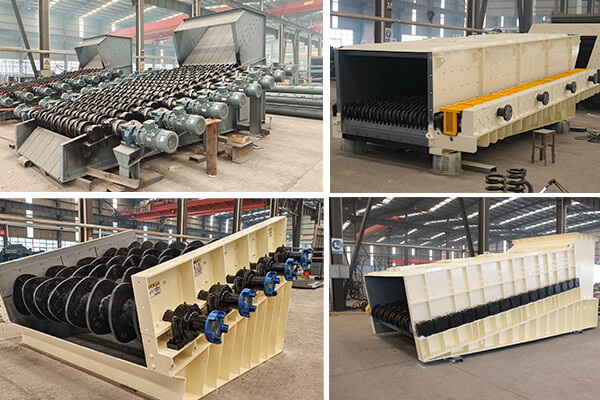
In the coal conveying system, the particle size of raw coal depends on the coal screening machine and the coal crusher, which are the key equipment causing the large size of the inlet lump coal. Therefore, the cause investigation should start from the coal screening machine and the coal crusher. 1.1 Technical Parameters of Coal Screening Machine and Coal Crusher ① Technical Parameters of the coal screening machine: The screening method is roller type, with 9 shafts and a shaft distance of 380mm; The inlet particle size is less than 300mm, and the discharge particle size of the under-screen material (hereinafter referred to as the discharge particle size) is 50m. The sieve hole size is 50mm x 80mm. ② Technical parameters of the coal crusher: The crushing method is ring hammer type: the output is 800t small h. Feed particle size ≤350mm; The output particle size is less than 30 mm.③ Belt width of the coal conveying system: 1200mm; Belt speed: 2 m/s; Conveying capacity: 800tho. According to the technical data, the maximum possible coal particle size (large side size) is less than 80mm, and there will be no large coal lumps that can break the belt of the belt coal feeder.
Due to the wear of components such as the screen plates of the coal screen and the hammer heads of the coal crusher during operation, the particle size of the output material will increase as the amount of equipment wear increases. The technical parameters of the coal screening machine and the coal crusher provided above are the initial parameters of the equipment. Therefore, it is necessary to inspect the on-site equipment. The maintenance personnel respectively opened the peeping holes of the coal screening machine and the coal crusher. No damage or excessive wear of the screen plates of the coal screening machine was found, nor was any damage or excessive wear of the hammer heads and coal crushing plates of the coal crusher found (the screen plates and hammer heads had been replaced recently). Large-sized coal lumps were collected for measurement at the outlets of the coal crusher and the coal screening machine. The coal particle size was all ≤50mm, while lumps larger than 50mm were mixed at the outlet of the
coal roller screen coal machine. Among them, two pieces of coal with dimensions of 48mm× 120mm×180mm and 50mm×123mm×164mm were collected. This indicates that large-grained lump coal comes from the coal roller screen coal machine. The screen surface structure of the coal roller screen coal machine is shown in Figure 1. The screen surface size is 1400mm×3420mm. There are 9 sets of screen shafts with a shaft distance of 280mm. There are 13 screen pieces on each shaft. The distance between two screen pieces is 50mm. The shape of the screen pieces is an 8-tooth plum blossom type. The outer diameter of the screen pieces is 330mm and the diameter is 130 mm. The tooth tops of the screen plates on the adjacent two shafts are aligned with each other. As can be seen from Figure 1, the coal roller screen coal machine has two types of screen holes. The space enclosed by four adjacent screen plates is referred to as Type A screen hole (50mm× 250mm), and the space enclosed by the connection line of the top of two adjacent coal roller screen coal machine plates and the screen wall plate is referred to as Type B screen hole (S0mm×1400mm). It can be seen from this that the coal particle sizes that can pass through the A-type sieve holes are: thickness < 50mm, width <250mm, and any length. The coal particle sizes that can be passed through the B-type sieve holes are: thickness <50mm, width <1400mm, and any length. Since the maximum particle size of thermal coal is generally limited to <300mm during procurement, the maximum particle size of lump coal that can pass through the sieve holes (underscreen materials) of the coal roller screen machine is: <50mm×250mm×300mm or <50mm×300mm×300mm. When the wear of the screen plate reaches the limit wear (i.e., the outer diameter of the screen plate is worn off by 20mm and the thickness of the screen plate is worn off by 5mm), the particle size of the undersize material will be larger, up to a maximum of 100mm×300mm×300mm. Therefore, it is necessary to carry out necessary renovations or repurchase of the coal roller screen coal machine to ensure that its output particle size is ≤50mm, thereby avoiding the belt of the belt coal feeder being scraped by large-particle lump coal.
Through the analysis of the structure of the coal roller screen coal machine, it can be known that the reason for the excessive particle size of the output material is that the screen plates of the coal roller screen coal machine are damaged or worn to the limit. If reordering a set of coal roller screen coal machines that meet the requirements of the coal feeder inlet is the most effective and quickest means, but from an economic perspective, it is not the most ideal method. Based on the principles of economy, safety and feasibility, this paper discusses whether the equipment can be appropriately modified. The key point of the modification is how to reduce the length dimension of the screen holes. As can be seen from Figure 1, the A-type screen holes are composed of four adjacent screen plates. If the screen plates on the adjacent screen shafts are staggered by A certain position, A new screen hole type can be obtained. The new screen holes are formed by two screen plates on the same axis and the top of one screen plate on the adjacent screen shaft. The width of the new screen holes remains unchanged, while the length is 12 of the original. The size of the screen holes is 50mm× 125mm. At this time, the maximum edge of the discharge particle size should be less than 125mm. ② As can be seen from Figure 1, the B-type associated hole is composed of the connection line of the top of two adjacent coal roller screen coal machine plates and the screen wall plate. If the diameter of the screen plate is increased until it is about to contact the screen plate of the adjacent roller, at this time, there is only one gap remaining at the top of the two opposite screen plates, and the B-type screen hole can be regarded as disappearing. From the above analysis, it can be known that the size of the A-type sieve holes has decreased and the B-type sieve holes have disappeared, thus achieving the purpose of reducing the sieve holes. Meanwhile, the output of the coal roller screen coal crusher has been reduced, increasing the crushing capacity of the coal crusher. However, from the technical data of the coal crusher, it is known that the crushing capacity of the coal crusher is 800th, and the conveying capacity of the coal conveying system is also 800t. It can be seen that the coal crusher has sufficient crushing capacity, and it is feasible to carry out the transformation according to this plan. In actual production, considering that the coal roller screen screen of the coal machine can still ensure the safety of the boiler belt coal feeder after moderate wear, while also taking into account factors such as not causing coal blockage in the coal roller screen coal machine due to the reduction of the screen holes, after analysis and calculation, it is more ideal to increase the diameter of the screen to 410mm. At this point, the screen plate has an ultimate wear limit of 20mm. After the screen plates of the coal roller screen coal machine were misaligned and the diameter was appropriately increased, the structure of the screen surface after the transformation is shown in Figure 2. The sieve hole size is 105mm in length and 50mm in width, and the sieve plate has a wear of 20mm. That is, when the diameter of the screen plate wears out by 20mm, it should be replaced or the diameter of the screen plate should be increased by other means. The screen surface of the
coal roller screen coal machine is composed of rollers equipped with screen pieces. Each roller is made up of several screen pieces strung on a straight shaft, and the screen pieces are connected to the shaft as a whole through keys. Each screen plate is composed of a hub and blades. It is an integrated casting and has interchangeability. From this, it can be seen that the equipment meets the basic conditions for transformation. During the renovation, it is only necessary to increase the diameter of the screen plates and misalign the screen plates on the rollers.