In the huge system of modern industrial production, the graded
mineral sizers is like an indefatigable "hercules", which undertakes the key task of material crushing and is widely used in many fields such as mining, metallurgy, building materials, chemical industry and so on. Whether it is hard ore, brittle coal or any other material that needs to be crushed, mineral sizer relies on its unique working principle and efficient crushing capacity to precisely break large blocks of material into the required particle size, laying a solid foundation for subsequent production processes. Its efficient operation not only improves production efficiency, but also reduces production costs to a certain extent, and becomes an indispensable key equipment in industrial production.
Among the many components of mineral sizer, the wear-resistant lining plate seems to be only a "small role", but it plays a pivotal role and is one of the key factors to ensure the stable operation and efficient work of the crusher.
Wear-resistant lining: the "shield" of the crusher
During the operation of the graded mineral sizer, the material will have a strong collision and friction with the internal components of the crusher at high speed and high pressure. The wear-resistant lining plate is like putting on a solid layer of "protective shield" for the crusher, which is closely attached to the parts vulnerable to wear of the crusher, such as the inner wall of the crushing chamber, the surface of the tooth roll, etc., and directly withstand the impact and friction of the material.
From the point of view of protecting the key components of the equipment, if there is no protection of the wear-resistant liner, the metal body of the crusher will be directly exposed to the impact and friction of the material. In a short period of time, the metal body may have serious wear, scratches and even deformation, which will greatly affect the normal operation of the crusher. The existence of wear-resistant lining effectively isolates the material from the metal body, making the key components reliably protected. For example, in some large mining projects, mineral sizer processes a large amount of extremely hard ore every day, and without wear-resistant lining, the core components of the equipment can be scrapped in just a few weeks due to excessive wear, and with the installation of wear-resistant lining, the service life of these key components can be extended by several or even tens of times.
Wear-resistant lining plays a key role in prolonging the service life of equipment. Because the wear-resistant lining itself has good wear resistance, it can maintain relatively stable physical properties and structural integrity under harsh working conditions for a long time. When it withstands the impact and friction of the material, the wear rate is relatively slow, so that it can continue to provide effective protection for the crusher. Taking a metallurgical enterprise as an example, after the use of the graded mineral sizer with high-quality wear-resistant lining, the overall service life of the equipment has been extended from the original 2-3 years to 5-8 years, greatly reducing the frequency and cost of equipment replacement.
Reducing maintenance costs is also one of the important roles that wear-resistant lining can not be ignored. On the one hand, because the wear rate of the wear-resistant liner is slow, the replacement cycle is long, which reduces the human, material and time costs caused by frequent replacement of parts. In the past, a building materials company did not use high-performance wear-resistant liner, almost every month need to inspect and replace the fragile parts of the crusher, consuming a lot of manpower and time, and replace with high-quality wear-resistant liner, inspection and replacement cycle extended to half a year or even a year, greatly improving production efficiency and reducing maintenance costs. On the other hand, because the key components are effectively protected, the shutdown maintenance time caused by equipment failure is reduced, and the economic loss caused by the shutdown is avoided. In modern industrial production, time is money, and each shutdown may bring huge economic losses to the enterprise. Wear-resistant lining boards indirectly save a lot of money for the enterprise by ensuring the stable operation of the equipment.
Material disclosure: common wear-resistant lining material
In the graded
mineral sizers, there are a wide variety of wear-resistant lining materials, each of which plays an important role in different working conditions with its unique performance characteristics. Next, let's have an in-depth understanding of several common wear-resistant lining materials.
High chromium cast iron: hardness and wear resistance of the strong
High chromium cast iron is a wear resistant material with excellent performance, and its chromium content is usually between 12% and 30%, and its carbon content is about 2.4% to 3.6%. From the perspective of chemical composition and organizational structure, it takes iron, chromium and carbon as the main components, and in the initial solidification state, the matrix is austenite, which is stable at higher temperatures and saturated by carbon (C), chromium (Cr) and other elements. As the temperature drops, the austenite body changes and eventually presents a multiphase structure dominated by austenite.
The key reason why high chromium cast iron performs well in the field of wear resistance is its unique wear resistance mechanism. On the one hand, the chromium element promotes the transformation of M3C carbides in white iron into M7C3 carbides. The hardness of M7C3 carbides is extremely high, up to HV1200-1600, which is much higher than the hardness of carburized carbides and common mineral abrasives, which makes high chromium cast iron can effectively resist the wear of materials. On the other hand, during the solidification process, the M7C3 carbides are rod-shaped and independently distributed, which not only improves the wear resistance of the material, but also enhances its toughness to a certain extent, avoiding the material embrittlement problem caused by the continuous distribution of carbides.
In practical applications, high chromium cast iron lining has obvious advantages in the treatment of high hardness materials. For example, in mining, for the crushing of quartz stone, basalt and other minerals with very high hardness, high-chromium cast iron lining can work stably for a long time with its high hardness and good wear resistance, greatly extending the replacement cycle of the lining board and reducing equipment maintenance costs. The relevant data show that under the same crushing conditions, the service life of high chromium cast iron liner is 2-3 times longer than that of ordinary liner.
High manganese steel: self-strengthening under impact
High manganese steel generally refers to the carbon content of 0.9% -1.3%, manganese content of 11.0% -14.0% cast steel, typical such as ZGMn13. It is a single austenitic structure between 1000-1100 ° C, and in order to maintain this organizational state, high temperature quenching is required, that is, water quenching to normal temperature immediately at the temperature between 1100-1050 ° C. After such treatment, high manganese steel has good toughness.
The wear resistance principle of high manganese steel is different from that of other materials, and it mainly relies on work hardening to improve wear resistance. When high manganese steel castings are subjected to impact load, plastic deformation will occur on the metal surface. Although the initial hardness of single-phase austenitic structure after water toughening treatment is low (HB170-230), with the occurrence of deformation, the deformed layer of the metal will appear obvious work hardening phenomenon due to the effect of deformation strengthening. The hardness of the surface layer (deformation layer) is greatly increased, which can reach HB500-800 (lower degree of impact can also reach HB300-400). From the surface inward, the degree of deformation of the metal gradually decreases, and the hardness also decreases, until the metal returns to the original undeformed state at a certain depth, and the work-hardened surface layer is the hardened layer.
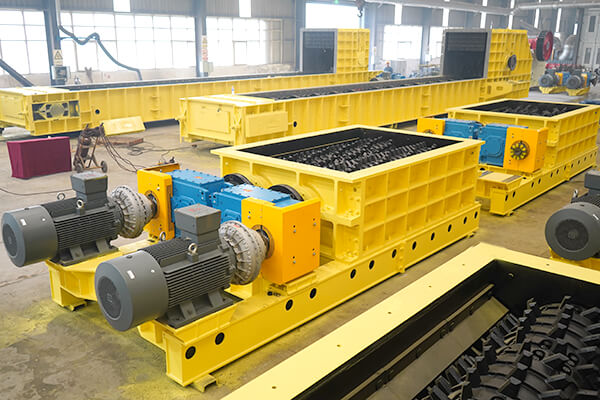
In dealing with the crushing of materials with high impact force, high manganese steel has shown significant advantages. For example, when the crusher deals with large, hard and large-impact materials, the high-manganese steel liner can quickly absorb the impact energy, and improve the surface hardness through work hardening, so as to effectively resist the impact and wear of the material. Taking a large quarry as an example, when mineral sizer of high manganese steel liner is used to break large blocks of granite, even in the face of frequent high-strength impact, the high manganese steel liner can still maintain good performance, the operating stability of the equipment has been greatly guaranteed, and the production efficiency has also been significantly improved.
Alloy steel: comprehensive performance of the play
Alloy steel is an iron-carbon alloy formed by adding an appropriate amount of one or more alloying elements (such as silicon, manganese, chromium, nickel, molybdenum, tungsten, vanadium, etc.) on the basis of ordinary carbon steel. The total amount of alloying elements is generally less than 5%, but the addition of these elements gives the alloy steel many excellent properties. From the perspective of chemical composition and organizational structure, different alloying elements play different roles in alloy steel, and they cooperate with each other to jointly change the crystal structure of steel, so that alloy steel has a variety of special properties.
Alloy steel has high strength and can withstand greater pressure and load, which makes it stable to support the liner structure during the operation of the crusher to ensure its normal work. Good corrosion resistance enables the alloy steel liner to maintain its structural integrity and performance stability in the face of moisture, acid and alkali and other corrosive environments, and extends the service life of the liner. Its wear resistance is also relatively good, can effectively resist the wear of materials. Alloy steel also has good processing and welding performance, which makes it more convenient and flexible in the manufacturing and installation process, can be processed into a variety of shapes and sizes of liner according to different equipment needs and working conditions, and can be firmly welded with other parts of the crusher to ensure the overall stability of the equipment.
In different working conditions, the alloy steel has shown good applicability. In some industrial production with high requirements for equipment operation stability and complex working conditions, such as chemical, electric power and other industries, alloy steel liner can give full play to its comprehensive performance advantages. In the chemical industry, the crusher may need to deal with materials containing corrosive media, at this time, the corrosion resistance and wear resistance of the alloy steel liner can ensure the normal operation of the equipment and reduce the number of equipment failures and maintenance caused by corrosion and wear.
Tungsten Carbide coating: Wear-resistant "special armor"
Tungsten carbide coating is a protective coating formed on the lining surface by a special process. The preparation process mainly includes thermal spraying, physical vapor deposition (PVD), chemical vapor deposition (CVD), laser cladding and other technologies. Taking thermal spraying technology as an example, tungsten carbide powder is heated to a molten or semi-molten state by a heat source, and is sprayed to the surface of the substrate at high speed to form a coating. In supersonic flame spraying (HVOF), the flame flow speed can reach Mach 5 (1500m/s) or more, which can prepare high-quality coatings with high bond strength and dense.
The principle of tungsten carbide coating to improve the wear resistance of lining plate is mainly based on its own high hardness characteristics. Tungsten carbide hardness is second only to diamond, has excellent wear resistance, can resist wear in long-term use, maintain good dimensional accuracy and surface quality. In tool manufacturing, tungsten carbide coated tools can still maintain sharp cutting edges under high-speed cutting and heavy load processing conditions, greatly extending the service life of the tool, this principle is also applicable to the wear-resistant lining plate of the crusher.
In addition to high wear resistance, tungsten carbide coatings also have good corrosion resistance and high temperature resistance. In terms of corrosion resistance, it can resist the erosion of a variety of chemical substances, including acid, alkali and other corrosive media, which makes the liner work normally in a harsh chemical environment. In the petrochemical industry, the lining plate of the crusher is often exposed to various corrosive chemicals, and the tungsten carbide coating can effectively protect the lining plate from corrosion and extend its service life. In terms of high temperature resistance, the melting point of tungsten carbide is as high as about 2870℃, which can maintain stable performance in a high temperature environment, so the tungsten carbide coated liner can also play an important role in some crusaders that need to operate under high temperature conditions, such as in the process of crushing high temperature materials in the metallurgical industry, it can ensure that the liner does not deformation, fall off and other problems at high temperatures. Ensure the stable operation of the crusher.
The adaptation of materials and application scenarios.
In the actual industrial production, the graded mineral sizer is faced with a variety of complex working conditions, and different material characteristics have a key impact on the choice of wear-resistant lining material. Only according to the hardness, humidity, viscosity and other characteristics of the material, reasonable selection of the appropriate material wear-resistant liner, in order to ensure the efficient and stable operation of the crusher, reduce equipment maintenance costs, improve production efficiency.
Hardness adaptation: hard to hard, soft to soft
For materials with higher hardness, such as quartz stone, basalt, etc., the Mohs hardness is usually above 6-7, which will have a strong wear effect on the lining plate during the crushing process. At this time, high chromium cast iron lining is a more ideal choice. The high hardness M7C3 carbides in high chromium cast iron can effectively resist the wear of these high hardness materials and maintain the good performance of the liner. In the crushing production line of some large mines, when dealing with extremely high hardness quartz stone, the service life of high-chromium cast iron liner is several times longer than that of ordinary liner, which greatly reduces the downtime and maintenance time of equipment and improves production efficiency.
For materials with low hardness, such as coal gangue, shale, etc., the Mohs hardness is generally about 3-4, and the wear of the lining board is relatively small. In this case, high manganese steel liner or alloy steel liner can meet the requirements of use. High manganese steel lining can be work hardened when subjected to a certain impact, which further improves its wear resistance, and has a good adaptability to materials with low hardness but certain impact. Alloy steel liner with its good comprehensive performance, in the processing of such materials can also show a stable working state. When mineral sizer is used to break coal gangue in a coal processing enterprise, high manganese steel liner is used. The equipment runs stably and the wear degree of the liner is within the acceptable range, which effectively guarantees the continuity of production.
Humidity considerations: Moisture resistance is important
When the material humidity is high, such as some wet ore, sludge, etc., it will not only increase the viscosity of the material, resulting in blockage during the crushing process, but also have a corrosive effect on the lining board. Under such conditions, it is important to select materials with good corrosion and wear resistance. Alloy steel lining has good corrosion resistance due to the addition of a variety of alloying elements, and can maintain stable performance in wet environment. Tungsten carbide coated lining also has excellent corrosion resistance and can effectively resist chemical attack in wet materials. In the sewage treatment plant, when mineral sizer is used to treat sludge, alloy steel liner or tungsten carbide coated liner can effectively extend the service life of the liner, avoid frequent replacement of the liner due to corrosion, and reduce the operating cost of the equipment.
Sticky response: anti-stick design and material combination
For the viscous materials, such as clay, some ores containing gum, etc., it is easy to adhere to the surface of the lining plate during the crushing process, affecting the crushing effect and the normal operation of the equipment. In addition to taking some anti-sticking measures in the structural design of the crusher, such as optimizing the tooth shape, increasing the surface roughness, etc., choosing the appropriate lining material can also play a certain role. The surface of the tungsten carbide coated liner is relatively smooth and has good non-stickiness, which can reduce the adhesion of viscous materials. In some ceramic raw material processing enterprises, when dealing with sticky clay, mineral sizer with tungsten carbide coating lining plate can effectively reduce material adhesion phenomenon, improve crushing efficiency and product quality.
In practical application, it is also necessary to comprehensively consider the working intensity, running time, production scale and other factors of the crusher, and make a reasonable choice of the wear-resistant lining plate quality. In some large-scale production mining enterprises, the crusher needs to run continuously for a long time, and the work intensity is larger, at this time, it is necessary to choose materials with better wear resistance and durability, such as high chromium cast iron or high-quality alloy steel, to ensure the stable operation of the equipment. In some small enterprises or intermittent production occasions, the cost control is more strict, you can choose more cost-effective materials according to the actual situation, such as ordinary high manganese steel or alloy steel.
Summary and prospect: the future road of wear-resistant lining
The wear-resistant lining of different materials plays a unique role in the graded
mineral sizers. High chromium cast iron, with its high hardness carbide and good wear resistance, performs well in the treatment of high hardness materials; High manganese steel shows its advantage in the crushing of high impact materials through the work hardening mechanism; Alloy steel is suitable for a variety of complex working conditions because of its good comprehensive properties. The tungsten carbide coating provides special protection for the lining with its high hardness, corrosion resistance and high temperature resistance. In practical application, according to the material characteristics, working conditions and other factors, reasonable selection of wear-resistant lining plate quality, can effectively improve the working efficiency and service life of the crusher, reduce the production and operating costs of enterprises.
Looking forward to the future, with the continuous progress of industrial technology and the increasing performance requirements of industrial production equipment, the quality of wear-resistant lining panels will also develop in the direction of more high-performance, multi-functional and green environmental protection. In terms of high performance, researchers will continue to explore new material formulations and preparation processes to further improve the hardness, toughness and wear resistance of the wear-resistant liner, so that it can work stably under harsher conditions for a long time. In terms of versatility, the future wear-resistant lining may integrate a variety of functions, such as in addition to excellent wear resistance, but also with self-healing, intelligent monitoring and other functions. The self-healing function can make the liner automatically repair when there is small wear or damage, thus extending the service life; The intelligent monitoring function can monitor the wear status, temperature, stress and other parameters of the liner in real time, and feed these data back to the operator in order to take maintenance measures in time to avoid the occurrence of equipment failure.
With the increasing awareness of environmental protection, green environmental protection will also become an important trend in the development of wear-resistant lining sheets. The future wear-resistant lining material will pay more attention to the conservation of resources and environmental protection, the use of renewable materials, reduce the use of harmful substances, reduce energy consumption in the production process will become the focus of research. Some new green wear-resistant materials, such as degradable polymer materials and wear-resistant materials prepared from waste, may gradually be applied in mineral sizer's wear-resistant lining plates, contributing to the sustainable development of industrial production.