Feeder breaker is mainly composed of crushing unit and conveying unit, both of which require the motor reducer to drive its operation. In the choice of reducer, you usually encounter the problem of choosing planetary teeth or gear box. This article will introduce the difference between the two and how to choose the reducer suitable for you.
The planetary reducer used for roller grinding often adopts the transmission structure of a parallel stage + intermediate row star + output row star. The intermediate level row star is between the parallel level and the output row star. In general, the sun wheel, the planet wheel and the inner gear ring of the intermediate star are straight teeth. In theory, it is not affected by the additional axial force generated by the front and back stage correlation structure, and no additional axial force is generated during its own operation. However, due to the existence of factors such as manufacturing errors, impact load bias, field installation tilt, and its own gravity, the intermediate stage planetary shelf still needs to design some axial positioning structures to avoid accidents caused by axial movement during operation. In the prior art, the intermediate stage planetary frame and the sun wheel with the output line star floating design, only the intermediate stage planetary frame axis position is installed on the top block, and the adjacent intermediate stage solar wheel and the secondary solar wheel are installed on the top block, the top block between the top block reserved a small amount of gap to prevent positioning, the axial momentum of the planetary frame is limited by the front and rear top blocks. As for the weight and partial load of the intermediate planetary frame and the planetary package, all rely on the free meshing force between the planetary wheel and the inner gear ring to bear.
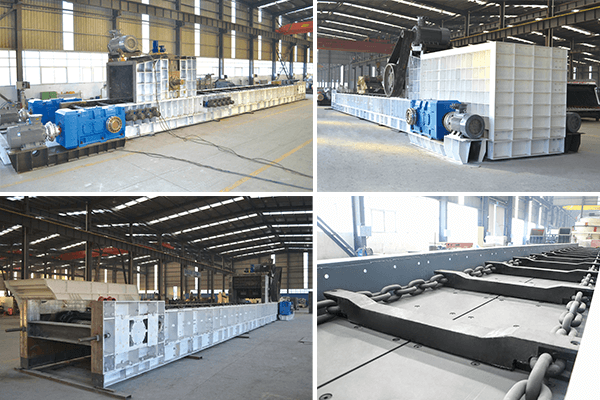
The invention provides a planetary gearbox and a planetary reducer, which can adapt to the working conditions of light load and heavy load, stable and reliable operation, high safety, the gearbox is not easy to be damaged, and the cost is low. The embodiment is as follows: On the first hand, our
feeder breaker uses a planetary gear box, comprising: A box, the box is provided with a first assembly hole, the first assembly hole is provided with a first bearing: [a bearing seat, the bearing seat is provided with a second assembly hole, the second assembly hole is provided with a second bearing: And the transmission mechanism, the transmission mechanism includes the input shaft, the first sun wheel, the inner gear ring, the planetary frame, the planetary wheel and the second sun wheel, the input shaft and the box rotationally connected, the first sun wheel and the input shaft transmission connection: The inner gear ring is connected with the box, the planetary frame is connected with the first bearing and the second bearing at the same time: The planetary wheel is connected with the planetary frame, and the planetary wheel is simultaneously engaged with the first sun wheel and the inner gear ring: The planetary frame is connected with the second sun wheel drive. In alternative embodiments, the housing comprises a first part and a second part, the first part, the inner gear ring and the second part are connected sequentially: The bearing seat is connected to the first part and the first assembly hole is arranged on the second part. In alternative embodiments, the first part, the inner gear ring and the second part are connected by bolts. The first part is provided with a positioning hole and the bearing seat is inserted into the positioning hole. The hole wall of the positioning hole is provided with a ring bulge, the bearing seat and the ring bulge are supported, and the bearing seat and the ring bulge are fixed by bolts.
Planetary gearbox provided by feeder breaker, the planetary frame is fixed on the box through the first bearing and the second bearing. During the operation of the planetary gearbox, the weight and partial load of the planetary frame and the planetary package in which it is located are borne by the first bearing and the second bearing, the planetary frame's movement in the axis is limited, and the gearbox runs smoothly. At the same time, the first sun wheel and the second sun wheel adopt a floating design in the axial direction, that is, the first sun wheel and the second sun wheel can produce displacement in the axial direction to offset the axial force, and the floating design of the two sun wheels play a regulating role in the average load of all levels of the sun wheel, and because only the sun wheel is set as a floating part, the sun wheel itself is small in size, light in weight, and small in axial movement. The positioning difficulty is low, the impact on the positioning block used to locate the axial movement of the sun wheel is small, the positioning block is not easy to be damaged, and the negative impact of the intermediate planetary frame and the floating of the planetary package is greatly reduced in the case of heavy load.
How to choose the reducer of the transmission unit of the
feeder breaker, mainly depends on the size of its reduction ratio to choose, the reduction ratio is relatively large, usually we choose the planetary gear reducer to achieve a reduction from the motor to the spindle, if the reduction is relatively small we choose the gearbox to achieve the role of deceleration.