- Improving processing and assembly process
Chain bucket elevator often has the phenomenon of chain plate falling off and cracking in the process of production. The reason for these phenomenon is that the assembly of pin roll and outer plate should fit tightly with larger interference, but the assembly precision did not meet the technical requirements in actual processing. Clearance coordination leads to the rotation of the pin roll relative to the outer plate and cuts the cotter, which is the fundamental reason of the outer plate falling off.
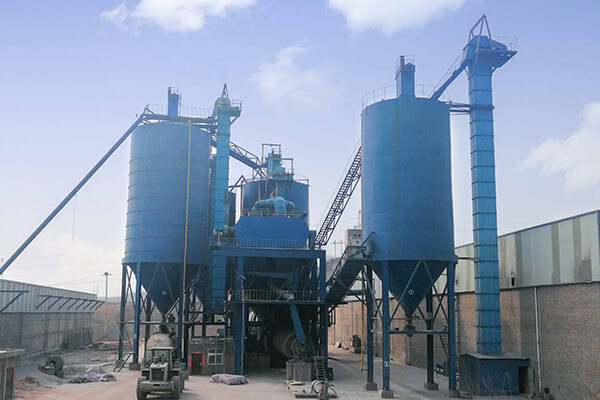
The handling method is to optimize the structure, and strengthen the manufacturing process, to ensure the parts processing and assembly accuracy. The punching of internal and external plate is divided into three procedures. The first is roughing, put the semi-finished product of the chain plate into the corresponding chassis mould, and punch out two holes at the same time with the coarse punching. Then change the chassis mould and replace the coarse punching with fine punching. Put the initial semi-finished product of the plate into the corresponding chassis mould and from the other side, carry out fine punching on the hole after rough punching. Finally, the chain plate was treated with shot blasting and heat treatment and thus the processing molding of chain plate is finished.
The assembly of the chain is that the cooperation of Inner chain plate and sleeve is transitionally fit and the cooperation of roller and sleeve is a slip fit, and assemble them into inner links. And assemble the inner link and pin roll with the outer plate to form a single link chain. The specific process is first assemble the roller on the sleeve, then press the inner chain plate into the sleeve or infiltrate the inner chain plate into the sleeve evenly with a hammer on the press machine, and then encase the pin roll into the pin roll hole of the assembled inner link, and finally the outer chain plate is pressed into the pin roll or evenly infiltrated into the pin roll with a hammer on the press machine. At the same time, the structure of chamfered edge of pin roll and sleeve is adopted, the assemble of pin roll and outer plate and sleeve and inner plate are adopted tight fit with large interference, which solve the relative rotation problem of pin roll and outer chain plate.
- Optimizing materials selecting and increasing fatigue resistance
When the
chain bucket elevator conveying the cement material with strong grinding performance, the hard material particles are easy to enter the gap between the sleeve and the pin roll, forming abrasive wear, which is the main failure mode of pin roll and sleeve. Due to improper material selection, most of the chain plate fracture, seriously affect the whole machine operation. Because the steel surface hardness is low, not wear resistance, under the action of alternating stress load, pin roll and chain plate surface easy to occur fatigue damage and finally fatigue fracture. Therefore, it is necessary to match the surface hardness of sleeve, pin rolland roller.
In view of the situation that crack occurs after quenching, the first step is to analyze the raw material. If there are cracks on the surface and inside of the raw material, they are not found before heat treatment, and quenching cracks may be formed. In addition, a double tempering program should be arranged in time to eliminate the stress in the internal structure in time to avoid the occurrence of cracks in the workpiece due to excessive residual stress in quenching. Due to improper cooling during quenching, cracking accidents will occur to the parts. Therefore, it is extremely important to select the appropriate cooling medium during quenching.