At present, for the opencast coal mine and the existing crushing station of the opencast mine, after the initial crushing, the material is transported to the secondary
mineral sizers by belt conveyor for crushing. The secondary crushing equipment usually involves two or more crushing equipment, and the corresponding screening equipment is required below. Because the conveying equipment (universal belt conveyor or other conveying equipment) and the related steel structure civil construction occupy a large area, and the secondary crushing requires a high steel structure or infrastructure foundation. Not only the equipment investment cost is very high, but also leads to the shortcomings of long installation and commissioning cycle, site applicability and poor equipment mobility, which restricts the rapid development of material mining in open pit mines to a large extent.
The purpose of our design is to provide an efficient screening type of large mineral sizers with its own separator, eliminating the intermediate link of the first crushing material being transported to multiple secondary mineral sizers by belt conveyor. The invention is installed directly under the primary mineral sizers and has the advantages of adjustable product particle size, compact structure, large crushing capacity, uniform material separation, easy removal and maintenance, low cost, low noise, easy installation and commissioning, high mobility, no civil construction, low steel structure foundation, small footprint, etc.
The utility model relates to a high efficiency screening type large mineral sizers with a feeding device, which comprises a crushing drive motor, a hydraulic coupling, a reducer, a double-drum gear coupling, a crushing box, a base support, a left tooth roller, a right tooth roller and a grease pump. The crushing drive motor, the hydraulic coupling, the reducer and the double drum gear coupling constitute a crushing drive unit. The crushing drive unit is two sets, which are respectively connected with the left tooth roller and the right tooth roller inside the crushing box. The dividing device comprises a dividing chute, an adjustable dividing rod, a movable connecting bracket, a dividing seat and a fixed connecting bracket: the fixed connecting bracket and the dividing seat are fixed on the crushing box of the crushing device, the dividing chute is fixed on the material output belt head outlet position, and the dividing chute is connected with the crushing box through the movable connecting bracket and a fixed connecting bracket.
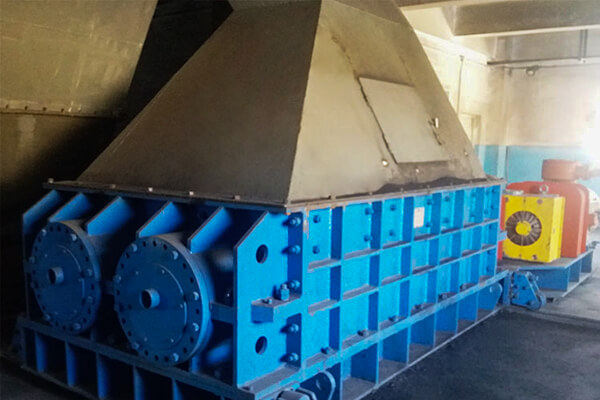
The double drum gear coupling comprises an inner gear sleeve of the reducer, a sealing disc, an outer gear sleeve of the left end, a safety pin, an inner gear sleeve of the tooth roller shaft, an expansion sleeve and an outer gear sleeve of the right end; The left tooth roller and the right tooth roller comprises a tooth plate, connecting screw, wedge block, tooth plate seat, tooth roller shaft, the tooth plate is fixed on the tooth plate seat through the connecting screw tightening wedge block, the wedge block and the tooth plate seat through the inclined plane to achieve the tooth plate tension; The output shaft of the reducer drives the inner gear sleeve of the reducer mounted on the shaft to rotate, the inner gear sleeve of the reducer engages with the left end of the outer gear sleeve, and is transmitted to the right end of the outer gear sleeve through the safety pin, and then the right end of the outer gear sleeve engages with the inner gear sleeve of the tooth roller, and the tooth roller and the inner gear sleeve of the tooth roller are connected together through the expansion sleeve on the tooth roller. Then drive the left tooth roller or the right tooth roller to rotate. The base support comprises a motor base, a reducer base, a support beam, a driven walking wheel set, a connecting beam and an active walking wheel set, and the motor base, the reducer base, a supporting beam and a connecting beam are welded as a whole; The crushing drive motor and the reducer are respectively fixedly connected with the motor base and the reducer base through high-strength bolts.
The left tooth roller and the right tooth roller reverse rotate in the center direction, and the material size adjustment range is 50~150mm. Positive and beneficial effects are as follows: 1. It is installed directly below the primary
mineral sizers, and the broken material after the primary mineral sizers is passed through the dividing device and the crushing device of the invention. After dividing the material, the secondary crushing work is completed in the same height plane without the need for redundant connecting equipment and infrastructure structure, which improves the crushing efficiency and reduces the equipment and production cost. It has the advantages of adjustable product size, compact structure, large crushing capacity, uniform material separation, easy removal and maintenance, low cost, low noise, easy installation and commissioning, high mobility, no civil construction, low steel structure foundation, small footprint and so on.
2. The dividing device comprises an adjustable dividing rod, a dividing chute, a movable connecting bracket, a fixed connecting bracket and a dividing pedestal. The material is evenly distributed to the axial direction parallel to the tooth roller through the dividing chute through the adjustable dividing rod, and then dispersed to the feeding area on both sides of the tooth roller through the dividing pedestal; The fixed connecting bracket and the dividing seat are fixed on the top of the crushing box, and the dividing chute is fixed on the outlet position of the output belt head. The dividing chute connects the mineral sizers with the movable connecting bracket and the fixed connecting bracket. When the invention needs maintenance, the movable connecting bracket is lifted and fixed with the dividing chute, and can be moved out of the crushing device for maintenance, convenient and fast; When working, drop the movable connection bracket to connect the distribution chute to the mineral sizers box to prevent material overflow.
3, the dividing device is not driven by power, relying on the material's own falling body impact, change the falling position of the material to achieve the purpose of dividing the material, and according to the different characteristics of the material entering, you can adjust the adjustable dividing rod position to achieve the best dividing effect; Through the coordination of the movable connection bracket and the fixed connection bracket, the crushing device can be freely moved out, making the maintenance equipment more convenient, daily maintenance more convenient, and avoiding the equipment failure caused by the maintenance of the equipment.
4, two teeth roll along the center direction reverse rotation, discharge particle size can be adjusted in a large range: Due to the reverse rotation of the two-tooth roller along the center direction, the number of discharge ports increases, and the material is distributed to both sides of the tooth roller by the dividing device. The smaller material blocks leak through the center area of the two-tooth roller or the inner crushing area on both sides of the box, and the remaining large materials are broken to the required materials through the crushing teeth and side teeth in the crushing area on both sides of the box, and then discharged from the discharge port.
5, our
mineral sizers two tooth roller adopts the press mounting method to install the tooth plate seat, which improves the installation quality and installation efficiency. The axial fixation of the tooth plate seat adopts one end of the shaft table positioning, the other end of the double nut locking, and the circumferential flat key positioning; The tooth plate is tightened by wedge tension, which is convenient to install and solves the problem of tooth plate loosening.