From the coal out of the mine to the washing, the first quality control equipment is two
vibratory separators, the 1401 and 1402, in the miscellany workshop. From the coal out of the mine to the washing, the first quality control equipment is two
vibratory separators, the 1401 and 1402, in the miscellany workshop. Due to the poor fixing of the bolt, it is particularly difficult for personnel to deal with it, thus prolonging the impact time of the accident and causing a very bad impact. In the past 20 years, the workshop technicians have studied and analyzed the phenomenon, formulated the transformation plan, and implemented it. Through practice, it has been proved that the transformation results are excellent and practicability is strong, and the problem has been solved effectively. The structure of the feed screen surface of the circular vibrating screen is divided into pipe beam, light rail screen and screen plate. The light rail screen is composed of two bottom plates and the light rail vertically cross welded. The two bottom plates are respectively placed on the two pipe beams, and the bottom plates are drilled with evenly distributed holes for the use of "U" type hoops between the lower part and the pipe beams, and the whole screen plate above is evenly distributed and fixed with 20 × 250 "straight bolts.
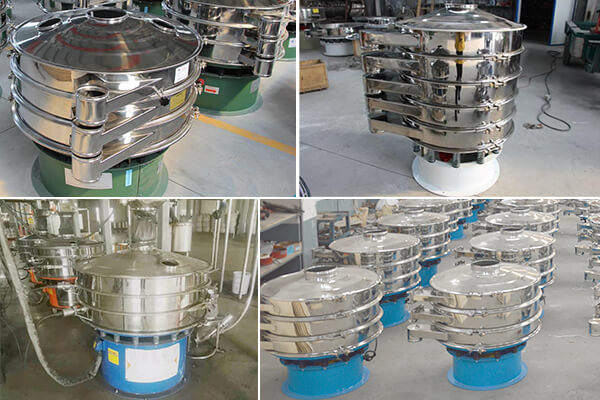
Condition before reconstruction
The distance between the screen surface and the bottom plate is about 200m completely connected by 20 screws. In the strong vibration, the screw is subjected to a large force, resulting in screw fracture, causing abnormal vibration and abnormal sound on the screen surface, while increasing the force of other screw, such a vicious cycle, eventually leading to the screen surface falling off. The equipment can not be suspended. In the strong vibration, the screw is subjected to a large force, resulting in screw fracture, causing abnormal vibration and abnormal sound on the screen surface, while increasing the force of other screw, such a vicious cycle, eventually leading to the screen surface falling off. The equipment can not be suspended.
When dealing with screw fracture fault, maintenance personnel can only reach into the lower part of the screen plate through the screen hole with a size of 80 on the screen surface, especially for the fixing bolt hole of the bottom plate. The field of vision is almost zero, which is difficult to alignment, thus greatly extending the fault processing time. According to statistics, the time of replacing a sieve plate fixing bolt is about one hour each time, which seriously affected the normal production of the mine.
Modification scheme
Because the roadway section and the rock hardness are large, the double wedge cutting method has better cutting effect in deep hole blasting. After the first-order cut blasting, under the comprehensive action of stress and detonation wave gas, the rock in the groove is broken and moved towards the working face, forming a funnel-shaped groove. A new free surface is created for the second order cut, and the clamping used by deep rock is changed accordingly, so that the strength is reduced, and it is beneficial to the blasting, crushing and movement of rock. At the same time, the residual stress in the rock and a large number of explosive fractures are caused to enhance the rock fragmentation.
The results show that the double wedge cut can increase the volume of the cavity and improve the depth of the cut, and the explosion heap is concentrated under the action of throwing, which is beneficial to rock loading. Double wedge cut blasting is adopted, and the interval time between first and second cut is 25ms. In the sequence of initiation, the first order cut hole is determined as one and the second order cut hole is determined as two.
After careful research and analysis on the structure of screen plate and light rail screen, we design "V" type perforated fixed bolt according to the appearance of "U "type collar and relevant size of screen plate, and the bolt is equipped with 180m pressure plate as matching nut.
Economic benefits
Before the reconstruction, according to statistics, there were at least 2 screw breaking accidents per month on average, and the processing time was more than one hour each time. After one year's practice, it has been proved that such accidents have been avoided. In this year, on the basis of ignoring the increase in power consumption, according to the coal output of the mine of 700T per hour, an extra 450T of washing raw coal should be put into the single system every month. Based on the calculation of 40% cleaned coal production rate of our factory last year, an extra 2160T of cleaned coal was produced in the whole year. Calculated at cleaned coal output of 1100 yuan /ton, the additional income was about 2.37 million yuan.
Above we introduced Modification of Securing Bolts for Screen Plate of Vibratory Separator. The HENAN EXCELLENT MACHINERY CO.,LTD is a professional bulk material conveying equipment manufacturer. We have professional production capacity and rich production experience as well as strict product quality inspection . We can guarantee that every equipment we produced is qualified equipment, and we ensure the qualified rate of the products. To know more about our products, Please visit our official website: https://www.exctmach.com/.