At present, the international commonly used
chain bucket elevator is vertical, according to the jb3926-85 standard, the most widely used is TD belt type, TH type ring chain and TB type board chain and other three types. This paper mainly introduce the selection principle of bucket elevator.
To select the machine according to the material’s moisture and viscosity. The front wall of the shallow hopper has a large slope and a small depth, which is suitable for transporting wet and poorly dispersed materials. The front wall of the deep Hopper has a small slope and a large depth, which is suitable for transporting dry and well-dispersed materials. These two hoppers are used in a bucket elevator with a sparse layout of the hopper. For the hopper with a guide edge, because when it bypasses the upper drum, the two-directional side of the front hopper is the unloading guide groove of the rear hopper, so it is suitable for conveying heavy and abrasive materials, which are used in the hopper for the dense arrangement of the bucket elevator.
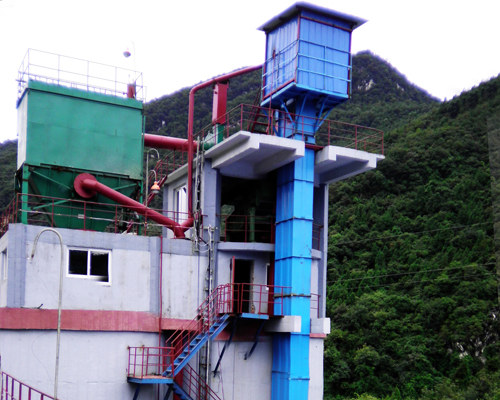
To select according to the lifting height and material temperature. Belt bucket elevator has the advantages of low cost and small quality, higher speed, smooth work and low noise, so it is widely used. However, due to the low strength of the tape, the hopper is fixed on the tape as a weak link, so its lifting height-the same is not too large, the type of transported materials are also limited.
Chain bucket elevator on the contrary, it allows for a large lifting height, can improve the block degree and higher temperature of the material. However, the chain drive will generate a dynamic load.
To select according to material characteristics and running speed. The extraction type is mainly used to transport powdery granular, small lumps of non-abrasive or semi-abrasive bulk materials, and many with centrifugal discharge with the application. Because there is no great resistance in the extraction of materials, the speed of the allowed items is high, typically 0.8~2.0/s. The inflow type is used to convey large chunks and finely crafted materials. The hopper is arranged in a dense setting to prevent the material from being scattered between the hoppers. The hopper runs at a lower speed, one. No more than 1 m/s. Therefore, it is mostly used in the bucket hoist of gravity unloading.
To select according to the material characteristics, running speed traction member. Centrifugal discharge is suitable for transporting powdery, granular and small block materials with good dispersion, and it is suitable for high-speed bucket elevator for evacuation arrangement of hopper, and it is mainly belt type.
Chain bucket elevator use less centrifugal discharge. The operating speed of centrifugal unloading hopper is usually 1 ~2/s, which has been selected to 5m/s. Gravity discharge is suitable for conveying bulk, heavy, abrasive materials and suitable for vertical or inclined bucket elevator with continuous arrangement of hopper. At this point the hopper runs at a speed of 0.4~0. 6/S, with a hopper with a guided edge. The scope of application of centrifugal-gravity (mixed) discharge is between the above two, often used to convey poor dispersion of powdery and moisture-containing materials, operating speed of 0.6~0.8/s.
To select according to process requirements. Because the traction member of the tilt bucket elevator needs to add the device to support the traction member when it is over, the structure is complicated, so the vertical bucket hoist is mostly used in general. When the vertical bucket elevator can not meet the special process requirements, it will adopts inclined bucket elevator.