The use of bulk in
dry mix mortar production line should be based on the scale of the project, the progress of the project and the type of mortar used to determine the quantity, distribution, arrival time and feeding schedule of the bulk
dry mixed mortar silos. The principle is that the project needs should be met, and the number of silos to be arranged should be economically reasonable. The number of silos should be as small as possible to meet the needs of the project.
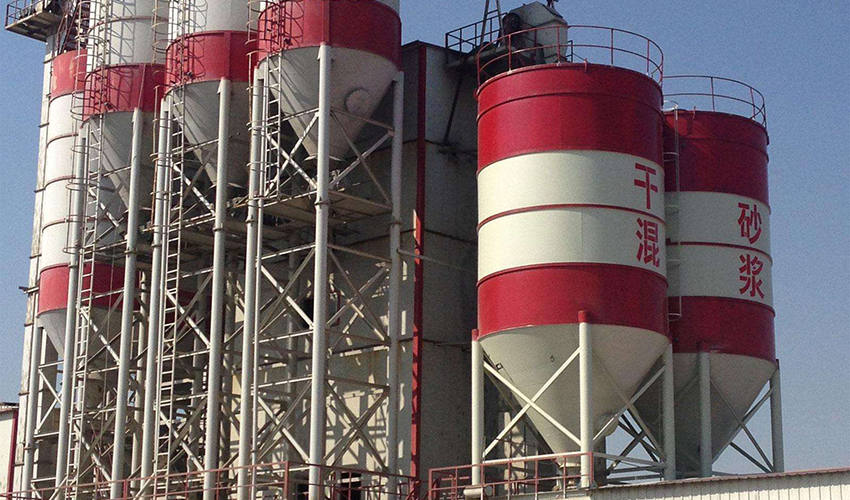
If the project is large in scale, there are many unit projects and there are many subcontracting units, then the number of dry and dry mortar silos should be more. It should be ensured that the silo and the construction operation surface should not be too long, otherwise the transportation distance will affect the construction efficiency. The use of bulk
dry mix mortar in dry mix mortar production line should not be too cumbersome, or it will increase the number of silos.
The number of silos should also be determined according to the progress of the project. In the initial stage of construction, the mortar demand is only in the masonry project, so as long as a small number of silos are provided to meet the engineering requirements, a 14m3 silo can be selected. If the project enters a large number of masonry stages, or the masonry project ends into the plastering stage, the number of silos should increase as the amount of mortar increases. The size of the silo can also be increased, such as 18m3, 20m3. It is possible to supply masonry mortar, interior wall plastering mortar and exterior wall plastering mortar at the same time. The number of silos should be gradually reduced during the construction closing phase.
The use of bulk dry mix mortar in
dry mix mortar production line should indicate the type of
dry mix mortar stored in the silo on the silo. Especially in the stage of plastering from masonry, it should be noted that when changing the type of mortar in the silo, the silo should be drained. When plastering the inner and outer walls at the same time, care should be taken not to confuse the variety of dry mortar, or it will cause a quality accident. For example, if the interior wall plastering mortar is misused to the outer wall, the mortar layer will be damaged after shelling, cracking or even peeling off after a period of use.
If the exterior wall plastering mortar is misused to the finished interior wall plastering layer, the external wall plastering mortar has higher shrinkage deformation and elastic modulus than the interior wall plastering mortar. The interior wall plastering mortar will cause the exterior wall plastering mortar to damage the inner wall plastering mortar, resulting in the bottom layer of the mortar layer and the shelling phenomenon of the base layer. If the interior wall plastering mortar is misused to the exterior wall plastering, it may also cause leakage of the mortar layer. Therefore, the mortar type identification of the on-site silo must be clear and accurate, and it is easy for the construction operator to master.
Before the silo is transported to the site of the construction site, the construction enterprise shall carry out the silo foundation construction according to the silo specification and the silo use manual. Brick foundations or reinforced concrete foundations can be used. The principle is to ensure that the silos do not tilt and tip over during field use, and that the silos are safe to use. The position of the silo in
dry mix mortar prodution line should be close to the working area, and it should also be close to the construction road in the silo area, so that the special bulk transport truck can be stopped for loading and unloading. Silos should have construction power and water supply, and the water source of the silo should have a pool to ensure the stability of water pressure.
.