In numerous fields such as mining and coal chemical production, the feeder breaker plays a crucial role. It can efficiently break large pieces of material into the required particle size, meeting the demands of subsequent production processes. Within the complex structure of the feeder breaker, the conveyor chain is an indispensable key component, serving as the "critical link" of the crusher.
From the perspective of material transportation, the conveyor chain acts as the "mover" of materials within the crusher. Once materials enter the crusher, the conveyor chain, through its continuous movement, smoothly transports the materials from the feed inlet to the crushing area. During this process, the stable operation of the chain ensures that materials can continuously and evenly enter the crushing chamber, preventing accumulation or blockage of materials and ensuring the continuous operation of the crusher. For instance, in large open-pit coal mines, a vast amount of large coal blocks need to be crushed and processed. The conveyor chain is like an efficient "material transport line", continuously delivering coal to the core crushing area of the crusher, enabling the entire crushing production process to operate efficiently.
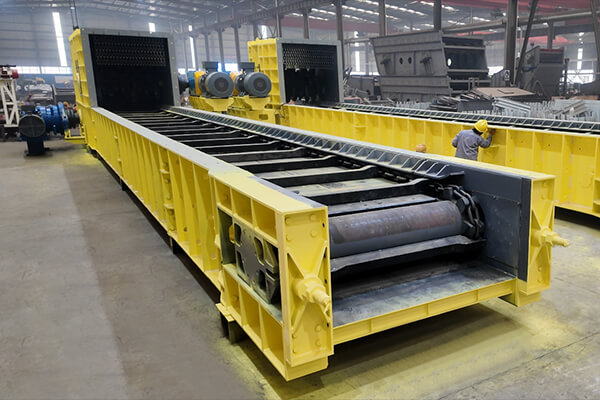
From the perspective of influencing crushing efficiency, the performance of the conveyor chain directly relates to the crushing efficiency of the crusher. If the chain lacks sufficient strength and poor wear resistance, it may deform or break under high-speed operation and the impact of materials. This not only interrupts material transportation but also causes frequent shutdowns for maintenance of the crusher, severely affecting production efficiency. Conversely, high-quality conveyor chains can adapt to high-intensity working environments, maintaining a stable operating speed and reliable conveying capacity, allowing the crusher to continuously and efficiently crush materials. Additionally, the operating speed and transmission accuracy of the chain also affect crushing efficiency. A reasonable operating speed enables materials to receive appropriate impact and compression within the crushing chamber, thereby improving the crushing effect; precise transmission ensures the stability of the chain's movement, avoiding uneven material transportation due to transmission errors and further enhancing the overall performance of the crusher. The conveyor chain plays a key role in material transportation and influencing crushing efficiency in the
feeder breaker. Selecting the appropriate chain is of great significance for ensuring the stable operation of the crusher, improving production efficiency, and reducing maintenance costs.
In numerous fields such as mining and construction material production, the feeder breaker plays a crucial role. It can efficiently break large pieces of material into the required particle size, meeting the demands of subsequent production processes. Within the complex structure of the feeder breaker, the conveyor chain plays an indispensable key role, serving as the "critical link" of the crusher.
From the perspective of material transportation, the conveyor chain acts as the "mover" of materials within the crusher. Once materials enter the crusher, the conveyor chain, through its continuous movement, smoothly transports the materials from the feed inlet to the crushing area. During this process, the stable operation of the chain ensures that materials can continuously and evenly enter the crushing chamber, preventing accumulation or blockage of materials and ensuring the continuous operation of the crusher. For instance, in large quarries, a vast amount of stone needs to be crushed and processed. The conveyor chain is like an efficient "material transport line", continuously delivering stone to the core crushing area of the crusher, enabling the entire crushing production process to operate efficiently.
From the perspective of influencing crushing efficiency, the performance of the conveyor chain directly relates to the crushing efficiency of the crusher. If the chain lacks sufficient strength and poor wear resistance, it may deform or break under high-speed operation and the impact of materials. This not only interrupts material transportation but also causes frequent shutdowns for maintenance of the crusher, severely affecting production efficiency. On the contrary, high-quality conveyor chains can adapt to high-intensity working environments, maintain a stable operating speed and reliable conveying capacity, enabling the crusher to continuously and efficiently crush materials. Additionally, the operating speed and transmission accuracy of the chain also affect the crushing efficiency. A reasonable operating speed can ensure that the materials receive the appropriate impact and compression within the crushing chamber, thereby enhancing the crushing effect; while precise transmission can ensure the stability of the chain's movement, avoiding uneven material conveyance due to transmission errors and further improving the overall performance of the crusher. The conveyor chain plays a crucial role in material transportation and influencing crushing efficiency in the feeder breaker. Choosing the right chain is of great significance for ensuring the stable operation of the crusher, increasing production efficiency, and reducing maintenance costs. A comprehensive overview of common conveyor chain types.
(1) Circular Chain
From a structural perspective, the circular chain is composed of individual circular links connected to each other, resembling a steel-cast circular bond. Its manufacturing process is rather complex. Firstly, high-quality alloy steel materials are carefully selected, which are like the high-quality foundation stones for building a skyscraper, laying the groundwork for the performance of the circular chain. After rigorous inspection and screening, the forging process begins. Under the influence of high temperatures and powerful forging forces, the raw materials are shaped into chain links of specific shapes and sizes. This process is akin to a craftsman meticulously carving an artwork, endowing the chain links with initial strength and toughness. The subsequent heat treatment process is even more crucial. Through quenching, tempering, and other techniques, it is as if powerful energy is injected into the chain links, further optimizing their organizational structure and performance, significantly enhancing their strength and hardness. For instance, in coal mine scraper conveyors, the circular chain, with its high strength, can stably pull the scraper, enduring the heavy pressure and friction of coal and other materials in harsh underground environments for long periods, ensuring efficient coal transportation. In feeder breakers, when dealing with hard ores, the high strength of the circular chain enables it to effectively resist the impact of materials, ensuring the continuous and stable transportation of materials to the crushing area; its excellent wear resistance also reduces the degree of wear during prolonged contact with materials, extending its service life, lowering equipment maintenance costs and downtime, and maintaining the efficient operation of the crusher.
Analysis of Key Factors Influencing Selection
(1) Material Characteristics
Material characteristics are one of the crucial factors influencing the selection of feeder breaker conveyor chains. They encompass various aspects such as material hardness, particle size, and moisture content. These characteristics act as "rulers" that precisely measure the performance requirements of the chains, thereby determining which type of chain is the best fit.
The hardness of the material directly tests the wear resistance of the chain. When a crusher processes hard materials such as quartz or granite, the material will cause intense friction and impact on the chain during the conveying process. If the chain lacks sufficient wear resistance, it is like a fragile shield unable to withstand a sharp spear, quickly leading to severe wear, with the chain links' surfaces peeling off, thinning, or even breaking, significantly shortening the chain's lifespan and increasing equipment maintenance costs and downtime. Therefore, when dealing with hard materials, it is necessary to choose chains made of materials with high hardness and excellent wear resistance, such as specially heat-treated alloy steel chains. Their surface hardness is greatly enhanced, effectively resisting material wear and ensuring stable material conveyance.
The size of the material particles also significantly affects the selection of chains. Large pieces of material exert considerable impact force on the chain during the conveying process due to their weight and inertia. This requires the chain to have sufficient strength and toughness to withstand such impacts. For instance, in large-scale mining operations, large chunks of ore extracted from underground need to be preliminarily crushed by crushers. At this time, the selected conveyor chains not only need to have large link sizes to ensure stable material carrying but also require high-strength materials. Chains with large-sized links and high-strength materials can easily handle the impact of large pieces of material, ensuring smooth material conveyance to the crushing area. Conversely, for smaller particle-sized materials, although the impact force is relatively small, the particles may penetrate into the connection parts of the chain, accelerating wear. Therefore, chains with tight structures and small gaps should be chosen to minimize material intrusion.
The moisture content of the material is also not to be ignored. When the material is highly moist, such as wet coal or clay, a water film forms on the surface of the chain, which not only accelerates the rusting of the metal chain but also may cause the material to adhere to the chain, affecting the normal conveyance of the material. In a humid environment, the metal reacts chemically with water, gradually corroding the chain and reducing its strength. The adhesion of the material increases the running resistance of the chain, leading to higher energy consumption and potentially causing chain jamming or disengagement. Therefore, for wet materials, chains with good anti-rust properties should be selected, such as those treated with zinc or chromium plating, whose metal coatings can effectively isolate moisture and slow down the rusting process; or stainless steel chains, which fundamentally enhance the chain's corrosion resistance and ensure stable operation in a wet material conveying environment.
(2) Working Environment
The working environment of the
feeder breaker serves as the "big stage" for the operation of the conveyor chain. Factors such as temperature, humidity, and corrosiveness, like various complex scenes on the stage, impose diverse and strict requirements on the material and performance of the chain.
In high-temperature environments, such as in cement plants' clinker crushers or steel mills' ore crushers, the surrounding temperature can often reach several hundred degrees Celsius. The impact of high temperature on the chain is multi-faceted. On one hand, high temperatures cause the metal material of the chain to soften, reducing its strength and hardness. Just as steel becomes soft and easily deformed at high temperatures, the chain is more prone to deformation and breakage when subjected to material impact and tension. On the other hand, high temperatures also accelerate the evaporation and aging of the chain's lubricant, increasing the friction between the links and further intensifying chain wear. Therefore, in high-temperature environments, it is necessary to select high-temperature resistant chain links. These chain links are typically made of special high-temperature alloy materials, whose microstructure remains stable at high temperatures, and they possess excellent thermal strength and oxidation resistance, enabling them to operate stably for long periods in high-temperature conditions.
High humidity working environments also pose challenges to chain links. In places such as underground mines and sand and gravel plants near water sources, the air humidity is relatively high, and moisture easily condenses on the surface of the chain links. If they remain in such an environment for a long time, the chain links are prone to rust and corrosion. Rusty chain links will have rust spots and pits on their surfaces, which not only affect their appearance but more importantly, weaken their load-bearing capacity and shorten their service life. Moreover, a humid environment may also breed mold and other microorganisms, which can attach to the chain links and further accelerate their damage. To address this issue, in addition to using anti-corrosion treated chain links as mentioned earlier, it is also necessary to enhance the ventilation and moisture-proof measures of the equipment, such as installing dehumidifiers and regularly drying the chain links, to reduce the erosion of moisture on the chain links.
When the working environment contains corrosive substances, the situation becomes even more severe. In the material crushing process of the chemical industry, various corrosive chemicals such as acids and alkalis are often encountered. These substances can react chemically with the metal of the chain links, causing corrosion. Different corrosive substances have different corrosion mechanisms and degrees on the chain links. For example, acidic substances can undergo displacement reactions with metals, causing metal ions to dissolve in the solution, resulting in holes and cracks on the surface of the chain links; alkaline substances may destroy the oxide film on the metal surface, accelerating the corrosion of the metal. To operate normally in such harsh environments, chain links with special corrosion resistance need to be selected, such as those made of acid-resistant stainless steel, nickel-based alloys, etc. These materials can form stable protective films in corrosive media, effectively resisting the erosion of chemical substances.
(3) Equipment Operating Parameters
There is a close and subtle relationship between equipment operating parameters and the selection of conveyor chain links. Parameters such as rotational speed, load, and conveying capacity are like the "passwords" of equipment operation, determining the performance requirements of the chain links. Only by accurately interpreting these "passwords" can the appropriate chain links be selected for the equipment.
The rotational speed of the equipment is one of the key parameters affecting the selection of chain links. When the rotational speed of the crusher is high, the number of movements of the chain links per unit time increases, which means that the impact and fatigue stress on the chain links also increase accordingly. Long-term operation at high speeds can cause fatigue fractures in the chain links, similar to how a rubber band loses its elasticity and breaks after being repeatedly stretched. Therefore, for high-speed crushers, chain links with good fatigue resistance need to be selected. These chain links are usually optimized in material selection and manufacturing processes, using high-strength and high-toughness materials, and through advanced heat treatment and surface strengthening processes, to enhance the fatigue strength of the chain links, enabling them to withstand the frequent impacts and alternating stresses brought by high speeds.
The size of the equipment load directly relates to the tensile force that the chain links must bear. In actual production, the crusher may encounter various load conditions, such as when processing large pieces of material or when the feed is uneven, the chain links may be subjected to instantaneous high loads. If the strength of the chain links is insufficient, they will not be able to withstand such high loads, resulting in the chain links being pulled apart or deformed. To ensure the safe operation of the chain links under various load conditions, it is necessary to select chain links of appropriate specifications and strengths based on the maximum load of the equipment. In the design and selection of chain links, a certain safety factor is fully considered to cope with possible sudden high loads, ensuring that the chain links have sufficient strength reserves to withstand various tensile forces during equipment operation.
Feeder breaker conveying capacity is also an important factor affecting the selection of chain links for feeders and breakers. A large conveying capacity means that more materials need to be conveyed within a unit of time, which requires the chain to have a higher conveying capacity and stability. On the one hand, the structure and size of the chain need to meet the requirements of large conveying capacity. For example, the width of the chain plate and the spacing of the chain links should be reasonably designed according to the conveying capacity to ensure that the materials can be conveyed smoothly on the chain without blockage or spillage. On the other hand, the operating speed of the chain also needs to be matched with the conveying capacity. Either too fast or too slow a speed may affect the conveying efficiency and the normal operation of the equipment. If the speed is too fast, the materials may be detached from the chain due to excessive inertia during the conveying process; if the speed is too slow, it will not meet the required conveying capacity for production. Therefore, when choosing a chain, it is necessary to comprehensively consider the conveying capacity and the operating speed of the equipment, and select a chain that can achieve efficient conveying while ensuring conveying stability.