The raw coal in our first mine is mainly lean coal and lean coal, and Xiaohuigou coal preparation Plant is a supporting coal preparation plant for the mine, with an annual selection capacity of 3.0Mt mountain. The coal preparation plant adopts the main re-separation of two products with pressure, the separation of coarse coal slime by interference bed separator and the separation of fine coal slime by flotation. Since the joint trial operation of the coal preparation plant, all the systems have been running normally and the product quality is stable. However, with the increase of faults and collapse columns in underground mining face, the gangue content in raw coal increases, and the recovery rate of cleaned coal is greatly reduced, which leads to serious clogging of raw coal system equipment, poor sorting effect of main re-sorting system, and inability to adapt to the deteriorating coal quality, which seriously affects the production efficiency and economic benefits of coal preparation plant.
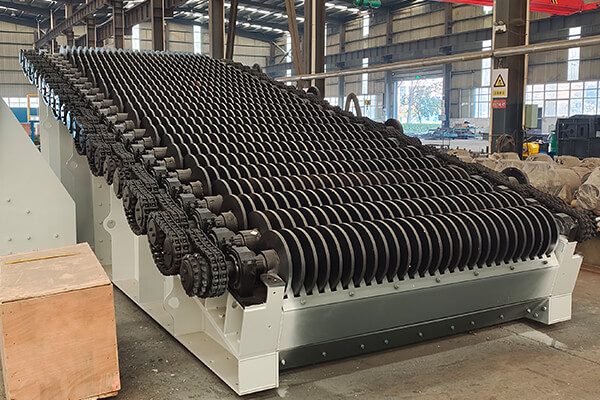
Coal roller screen is a kind of equipment specially used for raw coal screening, which has the advantages of large processing capacity, no vibration, low maintenance cost and low operating cost.
1 Problems Exist
Coal is crushed to less than 50mm after primary crusher, grading screen and secondary crusher. With the increase of bulk gangue in raw coal, the problems of raw coal preparation system and washing system gradually become prominent, as follows:
(1) There are more gangue in the raw coal of more than 50mm grain grade, and the hardness is large, and a large number of large gangue into the crusher leads to large load, more failures and large maintenance:
(2) The crushing size of bulk gangue cannot be guaranteed. Some gangue above 50mm enters the washing system, resulting in frequent stuck and blocked pipes and equipment, and serious stuck jam of the heavy cyclone pump, resulting in poor sorting effect, seriously affecting the processing capacity and sorting effect of the heavy medium production system:
(3) A large number of gangue into the main plant, resulting in serious wear of pipes and equipment;
2 Problem analysis The main coal seam of the mine is No. 2 coal, the coal is lean and lean coal, the gangue hardness is large, the coal is soft and fragile. Take mine coal for screening test), the results are shown in Table 1. As can be seen from Table 1:
(1) With the decrease of particle size, the ash content decreased significantly, and the ash content of 0.5~ 0mm grain grade was the lowest, which was 14.25%, indicating that the raw coal was brittle, the gangue was hard, and there was no obvious slime phenomenon.
(2) The ash content of raw coal is high, reaching 37.87%, of which large (4) gangue produces a large amount of high ash fine mud in the crushing process, which affects the ash content of cleaned coal.
The ash content of the block gangue is high, and the ash content of the grain grade above 50mm is 78.26%, indicating that most of the gangue above 50mm is small coal content. This part of bulk gangue after crushing into the washing system, increase the burden of washing system. Considering the transformation of raw coal system, the raw coal with less than 50mm grain grade will be discharged directly after sifting, which can greatly improve the washing efficiency and improve the washing effect.
3 Transformation Plan
3.1 Application of coal roller screen
In view of the small space of raw coal treatment system,
coal roller screen is selected as the raw coal classification equipment. coal roller screen is the use of screen shaft to drive multiple groups of screen disk rotation, to the screen surface of the material in the process of transport, larger than the size of the sieve sieve through the sieve plate, driven by the sieve shaft to one end of the movement and discharge from the end, less than the sieve hole of the material fell to the sieve plate, A mineral grading and screening equipment for separating materials according to different particle size levels 4). coal roller screen has the advantages of large processing capacity and low failure rate, especially suitable for raw coal classification. And the coal roller screen has no vibration parts, which can reduce the influence of dynamic load on the original coal bin in the minimum range.
3.2 Process flow after transformation
Remove the original raw coal grading screen and secondary crusher, the raw coal is crushed to less than 150mm in the wellhead room, and 50mm grading is carried out through the newly added coal roller screen on the original coal bunker; The raw coal larger than 50mm on the screen falls to the original bypass belt conveyor and enters the gangue bin for direct discharge. The raw coal less than 50mm under the screen falls to the belt conveyor and directly enters the original coal bin, and then enters the main plant for washing.
By increasing the coal roller screen on the original coal bin, the bulk gangue is removed in advance, the bulk gangue entering the production system is greatly reduced, the recovery rate of raw coal entering the washing is significantly improved, and the stability of the raw coal system and washing system is greatly improved.
(1) The coal preparation plant is operated by an outsourcing unit, and the washing processing fee is 14.6 yuan /t, and the bypass fee is 5.4 yuan /t. With 3 million tons of raw coal washed annually and 25% of the raw coal on the coal roller screen, the annual operating cost is saved by 6.9 million yuan
(2) After the transformation, the raw coal grading screen and secondary crusher are removed, and 1
coal roller screen are added to the warehouse, reducing 1 post worker. Annual savings of electricity and labor costs of 190,000 yuan.
(3) The stability of the raw coal system has been improved after the transformation, and the failure rate has been significantly reduced: the stability of the washing system has been greatly improved, the equipment wear and failure rate have been reduced, the processing capacity has been significantly increased, and the sorting effect has been significantly improved.