In the huge system of industrial production, the screening operation is like a key "Screen" To accurately separate and grade various materials, laying the foundation for subsequent processing processes. As an important equipment in the field of screening,
flip flow screen plays an irreplaceable role in many industries such as coal, metallurgy, building materials and chemical industry by virtue of its unique working principle and excellent performance. It can efficiently deal with all kinds of wet, sticky, fine and other difficult screening materials, and solve the problems of screen blockage and low screening efficiency that are easy to appear in the face of these materials in the traditional screening equipment.
The screen box, as the core component of the flip flow screen, is called the "Heart" Of the device. It not only carries key components such as screens and exciters, but also directly participates in the screening process of materials. The structural design, manufacturing process and material selection of the screen box have a decisive impact on the overall performance of the stretcher screen. A reasonably designed and well-manufactured screening box can ensure that the screen is stably relaxed during work, so that the material is fully rolled and beat on the screen surface, thereby improving the screening efficiency and accuracy. On the contrary, if there are defects in the screening box, such as insufficient structural strength, poor welding quality, etc., it may lead to deformation, cracking and other problems in the operation of the screening box, which not only affects the screening effect, but also may cause equipment failure, increasing maintenance costs and downtime. Therefore, an in-depth understanding of the processing process of the screen box is of vital significance for ensuring the high performance and reliability of the flip flow screen and improving the efficiency and quality of industrial production.
In the process of processing flip flow screen boxes, the selection of raw materials is like selecting a cornerstone for a magnificent building, and its importance is self-evident. Suitable raw materials are not only the basis for ensuring the quality of the screen box, but also the key factor in determining the overall performance and service life of the flanged screen.
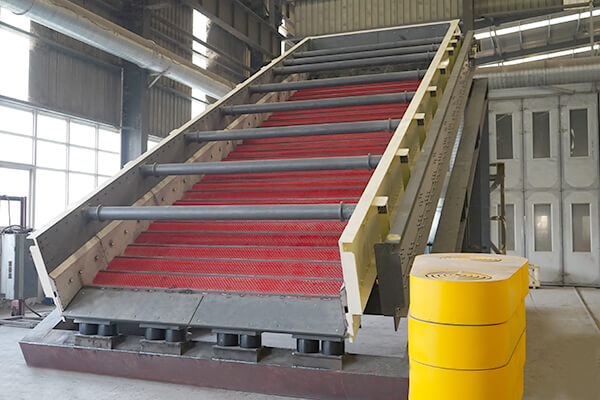
The main raw material of the screen box is steel, and the strength and toughness of the steel directly affect the vibration resistance and durability of the screen box. Generally, low-alloy high-strength structural steel such as q345b is selected. This steel has good comprehensive mechanical properties, high yield strength, and can withstand large external forces and vibration loads. When the sieve is stretched, it can still maintain a stable structure in the face of the impact of materials and the vibration of the sieve box itself, and is not easy to deformation or cracking. Taking coal screening operation as an example, in the long-term high-intensity working environment, the screening box needs to constantly withstand the impact and vibration of coal, q345b steel sieve box can rely on its excellent strength and toughness, stable operation, to ensure the continuous screening work.
In addition to the main steel, the connecting parts are also an indispensable part of the production of the screen box, such as high-strength bolts, nuts, etc. These connections should have sufficient strength and fastening properties to ensure that the connection between the components of the screen box is strong and that there is no loosening during the vibration of the screen box. If the quality of the connector is poor, the high-frequency vibration of the screen box may lead to the failure of the connection between the components, which will affect the overall structural stability of the screen box, reduce the screening efficiency, and even cause safety accidents. Therefore, when selecting the connector, it usually follows the relevant industry standards and strictly controls its quality to ensure that it meets the design requirements of the screen box.
As an important part of the screen box, the side plate of the screen box has strict requirements for its material flatness and thickness uniformity. The poor flatness of the side plate material will lead to problems such as uneven gaps and loose connections during the assembly of the screen box, which will affect the tightness of the screen box and the overall structural strength; however, the uneven thickness may cause the stress concentration phenomenon of the side plate during the loading, reduce the bearing capacity of the side plate, and easily cause the deformation or rupture of the side plate. Therefore, when purchasing side panel materials, it is necessary to carry out strict quality testing to ensure that the flatness and thickness uniformity of the material meet the design standards.
For some key parts of the screen box, such as the connection between the beam and the side plate under greater stress, strengthening materials will also be used for local strengthening to improve the strength and fatigue resistance of these parts. Reinforcing bars can be added to the joint or high-strength welding materials can be used for welding to enhance the strength of the connection part, so that it can better cope with various stresses in the work.
Before the
flip flow screen is processed, adequate preparation is the key premise to ensure the smooth processing and ensure the quality of the screen box. This stage covers two important aspects: Equipment preparation and drawing review.
There are many kinds of equipment required for processing screen boxes, and each assumes an indispensable task. Cutting equipment is used to cut raw materials into specific sizes and shapes according to design requirements, common plasma cutting machines, laser cutting machines and so on. The cutting accuracy of these devices directly affects the dimensional accuracy of each component of the screen box, and then affects the overall assembly accuracy of the screen box. When plasma cutting machine cuts thick steel plate, if the cutting parameters are not properly set, it may lead to a large roughness and perpendicularity deviation of the incision, which will affect the subsequent welding quality. Welding equipment is the key tool to connect various parts into a complete screen box, such as carbon dioxide gas shielded welding machine, argon arc welding machine, etc. Different welding processes and equipment are suitable for different materials and welding requirements, carbon dioxide gas welding machine is suitable for low carbon steel and low alloy steel welding, with high welding efficiency, low cost advantages; the argon arc welding machine is more suitable for welding stainless steel and other materials with higher welding quality requirements, which can ensure the beauty and strength of the weld. Drilling equipment is used to process a variety of connection holes and mounting holes on the screen box parts, common radial drilling machine, cnc drilling machine, etc. Its drilling accuracy and position accuracy are crucial for the assembly and subsequent use of the screen box.
After the equipment is ready, it is essential to debug the equipment. For cutting equipment, parameters such as cutting speed, cutting current, and gas flow need to be adjusted to ensure cutting accuracy and incision quality. When using a laser cutting machine to cut thin sheets, by precisely adjusting the laser power and cutting speed, the width of the incision can be controlled in a very small range, and the material utilization rate and processing accuracy can be improved. The debugging of welding equipment includes the adjustment of welding current, voltage, welding speed, wire feed speed and other parameters to ensure stable welding quality and avoid welding defects such as virtual welding, porosity and cracks. Taking carbon dioxide gas shielded welding as an example, suitable welding current and voltage can make the weld forming good, the penetration is moderate, and the stability of wire feeding speed can ensure the continuity of the welding process. Parameters such as drill bit speed and feed rate need to be adjusted to ensure that the dimensional accuracy and position accuracy of drilling holes meet design requirements. When using cnc drilling machine to process high-precision holes, by precisely setting machining parameters and tool paths, high-precision drilling can be achieved to meet the assembly requirements of screen boxes.
Drawing review is another core part of the preparation work before processing. The processing drawing of the screen box is the guiding basis for the entire processing process, which specifies the key information such as the structure, size, tolerance and technical requirements of the screen box in detail. When reviewing the drawings, first check the integrity of the drawings to ensure that the drawings contain all the necessary views, dimensioning, technical instructions, etc., and there are no omissions or ambiguities. Carefully check the dimensioning of each part of the screen box to ensure that it is consistent with the design requirements and the tolerance range meets the relevant standards. For some key dimensions, such as the thickness of the screen box side panels, the spacing of the beams, etc., any small deviation can affect the performance and service life of the screen box. Also review the technical requirements in the drawings, such as welding process requirements, surface treatment requirements, etc., to ensure that these requirements are feasible in the actual processing process and meet the relevant industry standards and specifications.
Plate cutting is the first process of screen box processing, and its cutting accuracy directly affects the subsequent processing and assembly quality, just as in the construction of tall buildings, accurate foundation measurement and cutting is to ensure that the building is a stable foundation. In practice, laser cutting and plasma cutting are two common cutting processes.
Laser cutting uses a laser beam with high energy density to irradiate the plate, so that the plate instantly melts or vaporizes, so as to achieve cutting. This cutting method has the advantages of high cutting precision, narrow incision, small heat affected zone, etc., especially suitable for cutting thin plates and parts with high precision requirements. When cutting some small holes on the side panel of the screen box, laser cutting can control the dimensional accuracy of the holes within ±0.1mm, and the surface roughness of the incision can also reach a low level, which provides good conditions for the subsequent assembly work. However, laser cutting equipment has high cost, relatively slow cutting speed, and limited cutting ability for thick plates.
The forming of structural parts is a key step in creating a solid "Skeleton" For the screen box, which determines the basic shape and structural strength of the screen box. Bending and stamping are the main processes for forming structural parts.
The bending process uses a bending machine to apply pressure to the sheet, causing it to undergo plastic deformation, resulting in the desired angle and shape. During the bending process of the side plate of the screen box, the bending angle and bending radius should be precisely controlled according to the design requirements. If the side plate needs to be bent to 90 degrees, the mold angle and pressure of the bending machine need to be accurately adjusted to ensure that the error of the bending angle is controlled within ±1 degree, so as to ensure that the side plate can be tightly fitted during assembly, and there is no problem of too large gap or angle deviation. In order to prevent the deformation of the structural parts during the bending process, some preventive measures are usually taken, such as pre-machining the plate before bending to remove the stress concentration on the surface of the plate; select the appropriate bending mold to avoid excessive friction between the mold and the plate resulting in scratches or deformation of the plate surface; in the bending process, the method of multiple bending is used to gradually reach the required angle and reduce the deformation of a single bending.
Stamping process is the use of punches and molds for rapid stamping of the plate, so that it is formed in a short time. This process is suitable for mass production of some structural parts with complex shapes, such as reinforcing bars and connecting parts on the screen box. During the stamping process, the design and manufacturing quality of the die directly affect the precision and quality of the stamping parts. A well-designed mold can ensure the dimensional accuracy and shape accuracy of the stamping parts, so that the stamping parts are highly consistent with the design drawings. At the same time, parameters such as stamping speed and pressure should be strictly controlled to avoid cracks, deformation and other defects caused by improper stamping parameters. Too fast stamping speed may cause the plate to be subjected to too much impact force in an instant, resulting in cracks; insufficient pressure may lead to incomplete stamping.
In the forming process of structural parts, quality control is an important link throughout. In addition to the strict control of the process operation, some detection means will be used, such as the use of measuring tools to measure the size of the formed structural parts to check whether they meet the design requirements; through the appearance inspection, check whether there are scratches, deformation, cracks and other defects on the surface of the structural parts. For some key structural parts with high size and shape requirements, high-precision testing equipment such as cmm will also be used for testing to ensure that its accuracy meets the overall assembly and use requirements of the screen box.
Welding assembly is the key link to connect the various processed parts into a complete screen box, just like the scattered building blocks into a strong castle, the quality of welding is directly related to the overall strength and stability of the screen box. In order to ensure the quality of welding, it is necessary to master certain operating skills in the welding process. Reasonable selection of welding current, voltage and welding speed is the key. Excessive welding current will lead to overheating of the weld, and defects such as edge biting and burning through. If the current is too small, it will cause problems such as incomplete welding and slag inclusion. The welding speed is too fast, the depth and width of the weld are insufficient, and it is easy to appear virtual welding. If the speed is too slow, it will overheat the weld and affect the welding quality. When welding q345b steel, according to the thickness of the plate and welding position, the welding current is generally between 100-200a, the voltage is between 20-30v, and the welding speed is controlled at 30-50cm per minute. Also pay attention to the welding sequence and direction, a reasonable welding sequence can reduce welding stress and deformation. Usually symmetrical welding, segmented welding and other methods are used to make the stress distribution in the welding process uniform and reduce the possibility of deformation of the screen box.
The processing process of
flip flow screen box is a systematic and rigorous process, covering a number of key links from material preparation, pre-processing preparation, to plate cutting, structural parts forming, welding assembly, parts processing, and then to quality inspection and surface treatment. Each link is related to each other and affects each other, which jointly determines the quality and performance of the screen box.